Residual stress (lattice strain) analysis
Residual stress analysis is built in in Maud, so you will not have to go through the whole theory of lattice strains like other before you. To make a long story short, Maud implements a residual stress analysis based on the work of S. Matthies.
This theory is based on an elastic model, and does include effects of lattice preferred orientations. It is quite similar to the theory proposed by Singh et al. (most commonly used in high pressure), but more advanced because
- it can refine more complex stresses that the pure axial case
- it does include effects of preferred orientations.
On the other hand, it does not deal with effect of plasticity on lattice strains, which can be an issue at high pressure.
Some useful papers
Link between lattice strains and axial stress, neglecting the effect of texture and plastic deformation (purely elastic theory)
- A.K. Singh; C. Balasingh; H.K. Mao; R.J. Hemley & J. Shu, Analysis of lattice strains measured under non-hydrostatic pressure, J. Appl. Phys., 83 , 7567-7575 (1998) doi:10.1063/1.367872
Link between lattice strains and axial stress, accounting for the effect of texture but neglecting plastic deformation (purely elastic theory)
- S. Matthies; H.G. Priesmeyer & M.R. Daymond, On the diffractive determination of single-crystal elastic constants using polycrystalline samples, J. Appl. Cryst., 34, 585-601 (2001) doi:10.1107/S0021889801010482
- S. Matthies; S. Merkel; H.R. Wenk; R.J. Hemley & H.K. Mao Effects of texture on the high pressure elasticity of iron from x-ray diffraction Earth Planet. Sci. Lett., 194 , 201-212 (2001) doi:10.1016/S0012-821X(01)00547-7
Effects of plasticity
- D.J. Weidner; L. Li; M. Davis & J. Chen Effect of plasticity on elastic modulus measurements Geophys. Res. Lett., 31 , L06621 (2004) doi:10.1029/2003GL019090
- L. Li; D.J. Weidner; J. Chen; M.T. Vaughan; M. Davis & W.B. Durham X-ray strain analysis at high pressure: Effect of plastic deformation in Mg O, J. Appl. Phys., 95 , 8357-8365 (2004) doi:10.1063/1.1738532
- S. Merkel; N. Miyajima; D. Antonangeli; G. Fiquet & T. Yagi Lattice preferred orientation and stress in polycrystalline hcp-Co plastically deformed under high pressure, J. Appl. Phys., 100, 023510 (2006) doi:10.1063/1.2214224
Analyzing stress and the effect of plasticity using self-consistent models
- S. Merkel, C. N. Tomé and H.-R. Wenk A modeling analysis of the influence of plasticity on high pressure deformation of hcp-Co, Phys. Rev. B, 79, 064110 (2009) doi:10.1103/PhysRevB.79.064110
- S. Merkel, M. Gruson, Y. Wang, N. Nishiyama and C. N. Tomé Texture and elastic strains in hcp-iron plastically deformed up to 17.5 G Pa and 600 K: experiment and model, Modelling Simul. Mater. Sci. Eng., 20, 024005 (2012) doi:10.1088/0965-0393/20/2/024005
Applying residual stress
 |  |
Residual stress options | Setting options in the stress model |
To have Maud apply residual stress analysis to your data
- in the main Maud window, select the phase that shows stresses
- edit it
- select the
Advanced models
tab
- it's all under
strain
...
For high pressure data, we usually use the following models
triaxial stress isotropic E
: you will have to know Young modulus and Poisson ratio,
moment pole stress
if you know the full Cij tensor,
Radial diffraction in the DAC
if the two above do not work or if you want to perform a more advanced analysis.
Refining a stress tensor (Triaxial Stress or Moment Pole Stress)
For those two cases, in the options
you will have to set the macrostresses. I usually use the following (options are accessible by click on the right button over each field)
s23
, s12
, s13
set to 0
s33
refined
s22 = -.5 s33
s11 = -.5 s33
This assumes that the stress is applied along the Z axis! If you are analyzing radial diffraction data and if you did make sure to read the section on "Define The Compression Direction", you should be OK. In compression, you will get negative values for s33
. It is expected since MAUD treats compressive stresses as negative.
To estimate the stress, simply refine
s33
s33
and the unit cell parameters
s33
, the unit cell parameters, and the beam center
and so on until you get a decent fit!!
You will get an estimate of stress. Now, do remember that this model is only as good as the physics behind it! Models for evaluating residual stress based on elasticity theory are known to fail if plastic deformation occur. If you are performing radial diffraction at high pressure and just want an order of magnitude, you will be OK. If you want anything more precise, or do not understand what I am talking about, read the papers above or contact an expert!!
More advanced model: radial diffraction in DAC
In most high pressure experiments, it has been noticed that the sine curve of the theory of Singh et al actually fits the data pretty well. In this case, you have
where
- psi is the angle between the diffracting plane normal and the maximum stress direction,
- d(hkl,psi) is the measured d-spacing for the hkl line at angle psi,
- dP(hkl) is the d-spacing for the hkl line under hydrostatic conditions,
- Q(hkl) is the lattice strain parameter for the hkl line.
In the elastic theory (e.g. Singh et al), you can calculate the differential stress using Q(hkl) and elastic constants. If you want to model the effect of plasticity using self-consistent models, you can use the values of Q(hkl) directly (see papers above).
In MAUD, the Radial diffraction in DAC stress model allows you to refine individual Q values for each diffraction line. At 300 K, in compression, and if you did make sure to read the section on "Define The Compression Direction", you should get POSITIVE values, on the order of 10^-3.
The angle alpha
, if optimized, is the angle between the maximum stress direction and the Z-axis. The angle beta
is the second angle defining the maximum stress direction (the angle between X and the projection of the maximum stress direction in the X-Y plane). You should refine those if, for some reason, your minimum d-spacings are not exactly at the azimuth where you expect them to be.
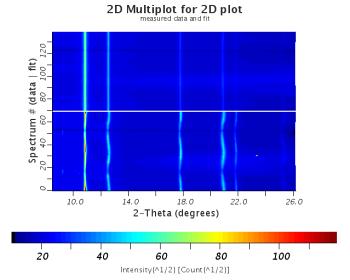 |  |
2-D plot before stress refinement | 2-D plot after stress refinement |